A Guide To The Code Of Practice For Respiratory Protective Equipment
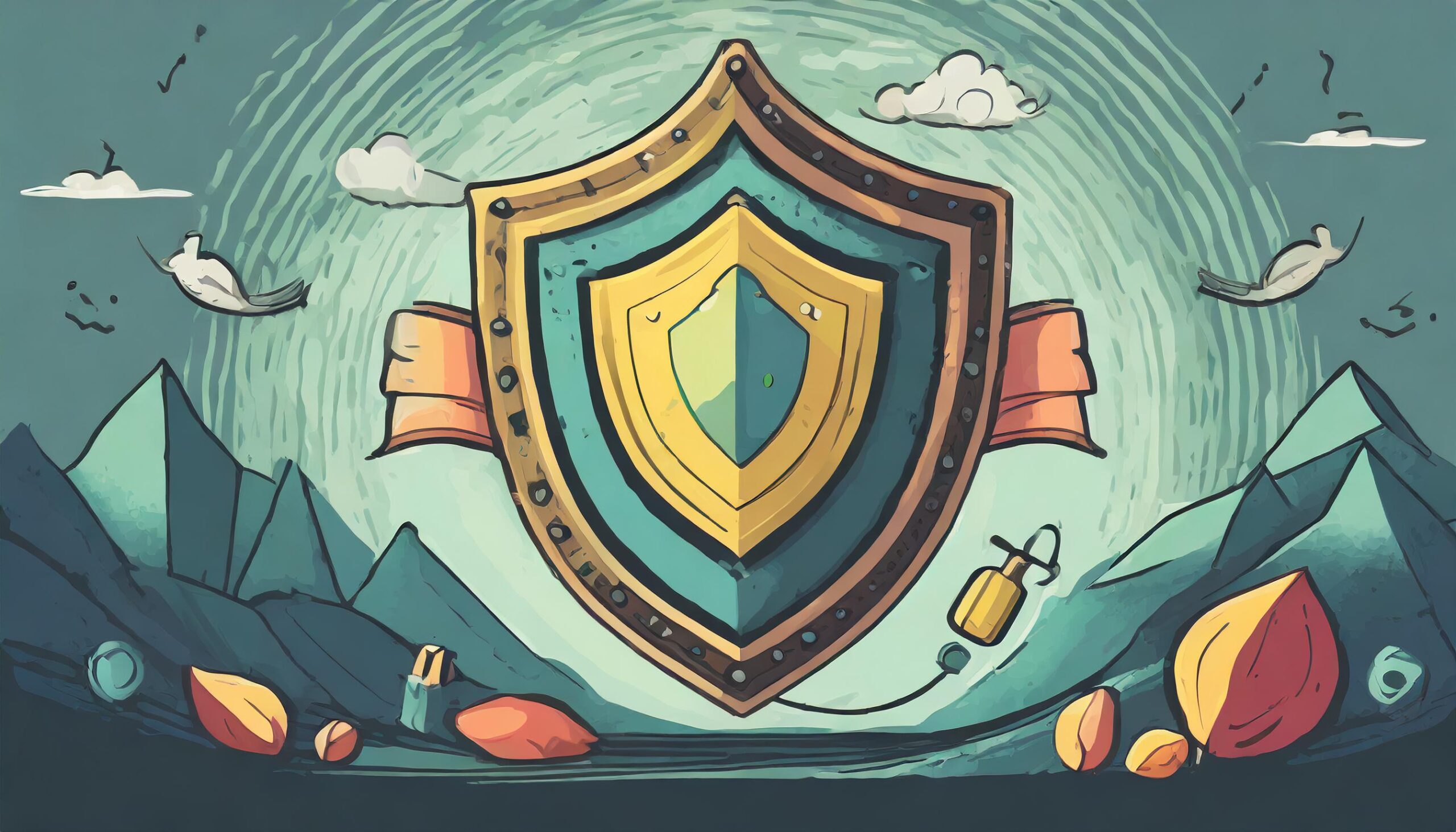
Quick Answer: The Code of Practice for Respiratory Protective Equipment outlines proper selection, use, and maintenance of RPE to safeguard worker health across various industries.
Key Takeaways:
- The Code of Practice for Respiratory Protective Equipment (RPE) provides comprehensive guidelines for selecting, using, and maintaining RPE to protect workers from airborne hazards across various industries, ensuring a uniform approach to respiratory safety.
- Proper selection and fit testing of RPE are crucial; they must match the specific hazards and work conditions, and fit testing confirms the equipment provides an adequate seal for effective protection against contaminants.
- Regular training and education for workers on the correct use, limitations, and emergency procedures of RPE, combined with adherence to legal and regulatory standards, are essential for maintaining a safe work environment and legal compliance.
When it comes to keeping safe on the job, especially where the air might not be, the Code of Practice for Respiratory Protective Equipment (RPE) is a beacon of guidance. This set of rules and recommendations is like a playbook for the workplace, ensuring everyone knows how to use RPE correctly. It’s not just about strapping on a mask; it’s about making sure that mask is the right fit, the right type, and used in the right way.
Organizations like the Occupational Safety and Health Administration (OSHA), the National Institute for Occupational Safety and Health (NIOSH), and the American National Standards Institute (ANSI) are the big players behind the scenes. They create and enforce these standards to keep workers from harm’s way when they’re in the thick of it, whether that’s dust, chemicals, or any airborne nasties.
Understanding the Code of Practice for Respiratory Protective Equipment
Definition and Scope of the Code of Practice
So, what exactly is the Code of Practice? Think of it as a rulebook that covers all the bases for RPE. It’s not just for one industry or one type of job. Whether you’re in construction, manufacturing, or healthcare, if you’re facing airborne hazards, this code has you covered. It outlines what equipment to use, how to use it, and when it’s necessary. The goal is to create a uniform approach to respiratory protection programs across the board.
The scope is broad, but it’s also specific. It doesn’t just say “wear a mask.” It dives into what kind of mask is needed for particular particles or gases, how to ensure a proper fit, and the maintenance required to keep equipment in top-notch condition. It’s about creating a safe environment for every worker, in every situation where the air might pose a risk.
Key Objectives and Benefits of Adhering to the Code
Following the Code of Practice isn’t just a good idea; it’s a crucial step in protecting worker health. The main goal here is to prevent respiratory illnesses and injuries that can happen when you breathe in something you shouldn’t. By sticking to the code, employers can also ensure they’re on the right side of the law, avoiding fines and legal issues that come with non-compliance.
But it’s not just about avoiding the bad stuff. There are real benefits to following these guidelines. For employers, it means a healthier workforce, fewer sick days, and a better reputation. For employees, it’s about going home at the end of the day in the same condition they came in, or even better, knowing they’re looked after. It’s a win-win situation.
Adhering to the code can also mean cost savings in the long run. Fewer health issues mean less spending on medical care and compensation. Plus, a strong safety record can lead to lower insurance premiums. It’s an investment in the future of the business and the people who make it run.
By understanding and applying the Code of Practice for RPE, workplaces can become safer, healthier environments. It’s about more than just compliance; it’s about taking care of the workforce and ensuring everyone has the protection they need to tackle their jobs with confidence.
Identifying Respiratory Hazards and Assessing Risks
Breathing is something we do without thinking, but when the air at work is laced with invisible threats, it’s a different ball game. Recognizing respiratory hazards is a crucial first step in safeguarding workers’ health. It’s not just about spotting the dangers; it’s about understanding them and knowing how much exposure is too much. That’s where risk assessment comes into play. This process helps us pinpoint the various airborne contaminants that could cause harm and set exposure limits to keep everyone safe.
Types of Airborne Contaminants and Their Effects
The air can carry a cocktail of gases, vapors, dust, fumes, and biological agents that each pose their own risks. Here’s a closer look at these unwelcome guests:
- Gases and Vapors: These can be sneaky, often invisible, and can range from mildly irritating to deadly. Think about carbon monoxide – it’s odorless but can be fatal.
- Dust: Not just an annoyance, dust can lead to chronic conditions like silicosis if inhaled over time.
- Fumes: Often produced during welding or similar processes, metal fumes can damage the lungs and nervous system.
- Biological Agents: These include bacteria, viruses, and fungi that can cause serious infections and diseases.
Understanding the health implications of each contaminant is vital for selecting the right RPE. It’s not just about strapping on a mask; it’s about choosing one that’s up to the task.
Conducting a Workplace Risk Assessment for Respiratory Hazards
A thorough risk assessment is like detective work. It involves identifying potential sources of respiratory hazards and evaluating the risk they pose. Here’s how it’s done:
- Walk-Around Surveys: Inspect the workplace, looking for processes or areas that might release contaminants.
- Employee Feedback: Talk to workers about the conditions they face and any symptoms they’ve experienced.
- Sampling: Collect air samples to measure contaminant levels.
- Expert Analysis: Have industrial hygienists and safety professionals review the data to determine the risks.
This assessment isn’t a one-time deal. It should be an ongoing process, adapting as conditions or processes change.
Establishing Exposure Limits and Air Quality Standards
Setting occupational exposure limits (OELs) is a science. It involves looking at data, considering the severity of health effects, and deciding how much of a contaminant workers can be exposed to without harm. Regulatory agencies play a big role in this, setting the standards that keep air quality in check.
These limits aren’t just numbers on a page; they’re benchmarks that help employers create safer workplaces. By sticking to these standards, businesses can protect their teams and steer clear of legal hot water.
In the end, it’s all about keeping the air at work as clean as the air we enjoy outside. With the right knowledge and tools, we can breathe easy knowing we’re protected from what we can’t see.
Selection and Implementation of Respiratory Protective Equipment
Choosing the right Respiratory Protective Equipment (RPE) is like picking the perfect shield in battle—it needs to be strong enough to protect you but suitable for the fight you’re in. The selection process should be meticulous, considering the specific hazards and work conditions to ensure workers are well-protected.
Criteria for Selecting the Appropriate RPE
When it comes to selecting the right RPE, several factors come into play:
- Nature of the hazard: Is the worker dealing with dust, chemicals, or biological agents?
- Level of protection required: What is the concentration of the hazard, and how toxic is it?
- Work environment: Will the RPE be used in a hot, humid, or confined space?
- Suitability: Does the RPE allow for the necessary range of motion and communication?
It’s not just about slapping on any mask and calling it a day. The RPE must match the specific needs of the situation to provide adequate protection.
Understanding Different Types of Respirators and Their Uses
There’s a whole arsenal of respirators out there, each designed for different scenarios:
- Air-purifying respirators: These filter out contaminants from the air. They come in disposable masks for less severe hazards, half-face respirators for moderate protection, and full-face respirators for more serious threats.
- Supplied-air respirators: These provide clean air from an uncontaminated source, ideal for environments with low oxygen levels or high toxin concentrations.
- Self-contained breathing apparatus (SCBA): Think of firefighters; SCBAs are for the most extreme conditions, providing a self-contained air supply.
Each type of respirator has its own set of applications, and it’s crucial to understand these to select the most appropriate one.
The Role of Fit Testing in RPE Selection
Even the best respirator is useless if it doesn’t fit properly. That’s where fit testing comes in. It’s not just a formality; it’s a critical step to ensure the RPE forms an adequate seal on the user’s face, providing the protection it’s designed to offer. There are two main types of fit testing:
- Qualitative fit test: A subjective method that relies on the user’s response to a test agent.
- Quantitative fit test: An objective method that measures the actual amount of leakage into the respirator.
Both methods are important to confirm that the selected RPE provides the necessary individual protection for each worker. It’s a personalized approach to a universal need—staying safe on the job.
By carefully considering the selection criteria, understanding the different types of respirators, and conducting proper fit testing, employers can implement an RPE program that stands up to the Code of Practice and, more importantly, keeps their workforce safe.
Proper Use and Maintenance of Respiratory Protective Equipment
Ensuring the safety of workers who rely on Respiratory Protective Equipment (RPE) goes beyond just providing the gear. It’s about making sure that the equipment is used correctly, maintained diligently, and stored properly. This not only extends the life of the RPE but also guarantees its effectiveness in protecting workers from respiratory hazards.
Donning, Doffing, and User Seal Checks
The process of putting on (donning) and taking off (doffing) RPE might seem straightforward, but it’s a procedure that requires attention to detail:
- Donning: Always inspect the RPE before use, adjust straps for comfort and fit, and ensure the mask is seated properly on the face.
- Doffing: Remove the RPE without touching the front of the mask or respirator to avoid contamination.
- User Seal Checks: Perform both positive and negative pressure checks to ensure there are no leaks.
These steps are crucial for RPE effectiveness. A poor seal can allow contaminants to bypass the filter, rendering the equipment useless and putting the user at risk.
Cleaning, Storage, and Maintenance Procedures
RPE requires regular care to function as intended. Here are some best practices:
- Cleaning: Disinfect the RPE after each use according to the manufacturer’s instructions to prevent the buildup of contaminants.
- Storage: Keep the RPE in a clean, dry place away from direct sunlight and extreme temperatures to prevent degradation.
- Maintenance Tasks: Replace filters and cartridges at the recommended intervals, and inspect for signs of wear and tear.
Proper maintenance ensures that the equipment remains in optimal condition, ready to protect workers whenever it’s needed.
Record-Keeping and Equipment Lifecycle Management
Detailed record-keeping is a vital part of managing the lifecycle of RPE. Records should include:
- Purchase Dates: To track the age of the equipment.
- Maintenance History: Documenting each cleaning, inspection, and repair.
- Fit Test Results: Ensuring the RPE continues to provide a proper seal for the user.
These records are invaluable for equipment lifecycle management and planning for replacement. They help to ensure that RPE is always in good working order and that workers are using equipment that meets the necessary safety standards.
By following these guidelines for the use, maintenance, and management of RPE, employers can uphold the Code of Practice and provide a safer work environment for their employees.
Training and Education for RPE Users
The effectiveness of Respiratory Protective Equipment (RPE) hinges not just on the quality of the equipment but also on the knowledge and skills of the people using it. That’s why comprehensive training programs are not just helpful; they’re absolutely necessary. These programs should cover everything from correct usage to understanding the limitations and handling emergency situations.
Developing a Comprehensive RPE Training Program
A well-rounded RPE training program should be as engaging as it is informative. Here are some key components:
- Hands-on Demonstrations: Nothing beats practical experience. Users should practice putting on, adjusting, and taking off RPE.
- Fitting Instructions: A good fit is crucial. Training must include how to achieve and test for a proper seal.
- Recognition of Malfunctions: Users should know how to spot problems with their equipment and what to do if they occur.
- Competent Trainers: Knowledgeable instructors are essential. They ensure that the training is accurate, up-to-date, and effective.
- Retraining: Skills fade over time. Regular refresher courses keep knowledge fresh and correct bad habits.
Training isn’t a one-time event. It’s an ongoing process that adapts as standards evolve and new equipment becomes available.
Instruction on Correct Usage and Limitations of RPE
Workers need to understand not just how to use RPE, but also its boundaries. Training should cover:
- Correct Use: Detailed instructions on how to use RPE properly in various situations.
- Respirator Limitations: Every type of RPE has its limits. Users must know what their equipment can and cannot do.
- Usage Guidelines: Adhering to these ensures that the RPE can provide the level of protection it’s designed to offer.
Knowing the capabilities and constraints of their RPE empowers workers to use it effectively and stay safe.
Emergency Procedures and RPE
In an emergency, the right knowledge can make all the difference. That’s why training must include:
- Respirator Failure: How to recognize it and what steps to take.
- Exposure Incidents: Procedures for dealing with unexpected contact with hazardous substances.
- Safety Training: Emergency procedures should be a staple of overall safety training.
By preparing for the worst, workers can remain calm and respond correctly during an incident. This preparation is a key part of any safety strategy and is essential for the well-being of everyone in the workplace.
Legal and Regulatory Compliance
Navigating the legal landscape of workplace safety can be as complex as it is critical. For those in industries where air quality is a concern, understanding and adhering to OSHA standards for respiratory protection is not just good practice—it’s the law. Employers and employees alike have a shared responsibility to ensure that the use of Respiratory Protective Equipment (RPE) meets these stringent requirements.
Overview of OSHA Standards for Respiratory Protection
OSHA standards set the bar for respiratory safety in the workplace. Key among these standards is the mandate for a written respiratory protection program. This program should outline the procedures for selecting and using NIOSH-certified equipment, conducting fit tests, and training employees on the proper use of RPE.
Employer and Employee Responsibilities Under the Law
Both employers and employees have distinct roles to play:
- Employer Responsibilities: Providing appropriate RPE, ensuring it is maintained, and training staff on its use.
- Employee Responsibilities: Using the RPE correctly and following the established safety procedures.
Failure to meet these responsibilities can lead to serious consequences, including fines and increased liability for employers, and health risks for employees.
Documentation and Compliance Auditing
Keeping detailed records is essential for demonstrating compliance with respiratory protection standards. These records should include:
- Training logs: Who was trained, when, and on what equipment.
- Fit test results: Documenting the effectiveness of the RPE for each user.
- Maintenance and inspection logs: Showing regular checks and any repairs or replacements.
Both internal and external audits are crucial for verifying that the practices align with the code of practice and legal requirements. Regular audits help identify areas for improvement and ensure that the workplace remains a safe environment for all.
By maintaining a clear understanding of these legal and regulatory frameworks, organizations can ensure they are protecting their workforce effectively and operating within the bounds of the law.
Monitoring and Evaluating RPE Program Effectiveness
To maintain a high standard of respiratory safety, it’s essential to regularly monitor and evaluate the respiratory protection program. This isn’t just about ticking boxes; it’s about ensuring the health and safety of every individual who relies on RPE to do their job safely. By using specific metrics and indicators, organizations can measure success and identify areas for continuous improvement.
Setting Up an RPE Program Evaluation Plan
An effective evaluation plan for an RPE program should be as robust as the equipment it assesses. It includes:
- Establishing benchmarks and performance indicators that reflect the goals of the program.
- Collecting and analyzing data to assess how well the program is working.
This could involve tracking the number of respiratory-related incidents before and after the program’s implementation or measuring the consistency of RPE usage across the workforce.
Indicators of a Successful Respiratory Protection Program
Several key indicators signal the success of a respiratory protection program:
- A reduced incidence of respiratory-related illnesses.
- High compliance rates with RPE usage guidelines.
These indicators help organizations to make informed decisions about where to focus their improvement efforts.
Continuous Improvement and Updating RPE Practices
The field of respiratory protection is always advancing, with new technologies and changes in regulations. Companies like MasVida Health understand the importance of staying current. They offer services like same-day oxygen delivery and FDA-certified transfilling to ensure that healthcare providers can maintain the highest quality of care without the worry of equipment shortages or outdated practices.
For a respiratory protection program to remain effective, it must evolve. This means:
- Keeping abreast of technological advancements and integrating them into the program.
- Adapting to regulation changes to ensure ongoing compliance.
By committing to continuous improvement, organizations can ensure that their RPE practices not only meet current standards but set new ones for respiratory safety in the workplace.
Frequently Asked Questions
Question 1: What are the consequences for non-compliance with the Code of Practice for RPE?
Answer: Non-compliance can result in legal penalties, increased liability for employers, health risks for employees, and potential OSHA fines.
Question 2: How often should fit testing be conducted for RPE?
Answer: Fit testing should be conducted at least annually or whenever there is a change in the type of RPE used or the user’s physical condition.
Question 3: Can employees use their own RPE if they prefer it over what the employer provides?
Answer: Employees can use their own RPE if it meets OSHA standards and is approved by the employer as part of the respiratory protection program.
Question 4: Are there specific training requirements for employees who use RPE?
Answer: Yes, OSHA requires comprehensive training on proper RPE usage, limitations, maintenance, and emergency procedures.
Question 5: How should RPE be stored to ensure it remains effective?
Answer: RPE should be stored in a clean, dry place away from direct sunlight and extreme temperatures to prevent degradation.
Join healthcare’s ultimate resource for long-term care!
Never miss out on our podcast, blogs, or daily content created to educate, equip, and encourage long-term care leaders to provide better care to the growing population of over eight million seniors in the U.S.
• Follow Us on Linkedin
• Join our weekly Newsletter
OneSource: Your Single Source for Same-day DME Delivery and Better Facility Hygiene
Better products. Better service. Better outcomes.
Partnering with one provider for your DME and facility hygiene services can result in reduced turnover, higher quality work, and healthier facilities.
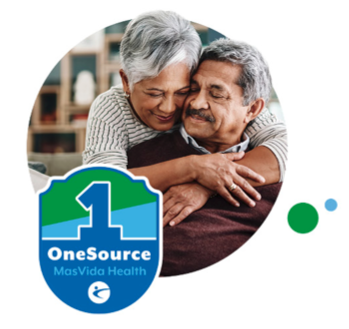

Medical OxygenTherapy →
Negative Pressure (NPWT) →
Respiratory Therapy →
Durable Medical Equipment →