Creating A DME Cleaning Schedule
Quick Answer: To establish a DME cleaning schedule, identify equipment types and their specific cleaning needs, determine cleaning frequency based on usage and risk, and implement regular documentation and revisions.
Key Takeaways:
- Establish a tailored DME cleaning schedule by identifying the specific types of equipment in your facility, understanding their unique cleaning requirements, and determining the appropriate frequency of cleaning based on usage and risk of infection.
- Implement effective cleaning protocols by following manufacturer guidelines, using suitable disinfectants, and ensuring all staff are trained on the correct procedures to maintain compliance and prevent cross-contamination.
- Leverage technology to enhance DME management, utilizing tools like real-time tracking and automated scheduling to ensure equipment is maintained efficiently and meets health standards, thereby improving patient safety and operational effectiveness.
Establishing a DME Cleaning Schedule
Creating a comprehensive DME cleaning schedule is crucial for maintaining the hygiene and safety of medical equipment in nursing homes and long-term care facilities. Understanding the types of equipment, their usage frequency, and the risks associated with inadequate cleaning are foundational steps in this process. This guide will help administrators assess the cleaning needs based on these factors and set up a schedule that ensures all equipment is consistently maintained in a hygienic condition. Additionally, incorporating practices for documenting and revising the cleaning schedule will keep the process dynamic and responsive to changes in equipment or facility needs.
Identifying DME Types and Their Specific Cleaning Needs
Different categories of DME, such as respiratory equipment, mobility aids, and hospital beds, are commonly found in care facilities. Each type has unique cleaning requirements influenced by its material composition and usage patterns. For instance, respiratory equipment, which comes in direct contact with patients, requires more frequent and meticulous cleaning to prevent infections. On the other hand, mobility aids like walkers and wheelchairs might need less frequent but equally thorough cleaning to remove dirt and potential pathogens.
To effectively manage these needs, categorize your equipment and outline specific cleaning protocols for each category. This approach helps in preventing cross-contamination and ensures patient safety. For example, using disinfectants suitable for electronics on respiratory machines, while opting for more robust cleaning agents for metal-based mobility aids, can be part of your tailored cleaning protocols.
Determining Cleaning Frequency Based on Usage and Risk
The cleaning frequency of DME should be determined by factors such as level of patient contact, risk of infection transmission, and manufacturer guidelines. Equipment that is used more frequently or has higher patient contact should be cleaned more often to minimize infection risks. For example, items used in patient rooms like hospital beds or certain respiratory aids should be cleaned daily, whereas equipment used less frequently might be scheduled for weekly cleaning.
Develop a cleaning timetable that aligns with these risk assessments and adheres to health standards. This not only enhances patient care but also ensures compliance with regulatory requirements. Regular reviews of the cleaning schedule, guided by changes in equipment usage or updates in health protocols, will further optimize the hygiene practices in your facility.
By systematically assessing the types of DME, their specific cleaning needs, and appropriate cleaning frequencies, administrators can establish a robust cleaning schedule. This schedule should be well-documented and regularly updated to adapt to any new health standards or changes in the facility’s operational needs. Partnering with a provider like MasVida Health Care Solutions can simplify the management of your DME needs, ensuring that your equipment is not only delivered on time but also maintained according to the highest standards of hygiene and safety.
Implementing DME Cleaning Protocols
Proper cleaning of Durable Medical Equipment (DME) is not just a necessity; it’s a requirement. Following manufacturer guidelines and adhering to regulatory compliance are fundamental to ensuring the safety and effectiveness of cleaning procedures. This section will guide you through the essential steps for cleaning, disinfecting, and storing DME, emphasizing the use of appropriate cleaning agents and equipment. Additionally, we’ll tackle common challenges and offer troubleshooting tips to enhance your cleaning practices.
Step-by-Step Cleaning Procedures for Various DME
Effective cleaning of DME involves several critical steps: pre-cleaning, cleaning, and post-cleaning. Here’s how to manage each stage:
- Pre-Cleaning: Remove any visible dirt or residue. This might involve wiping down surfaces with a soft cloth or using a gentle brush to dislodge particles.
- Cleaning: Use the recommended cleaning agents and follow the specified techniques to ensure thorough disinfection. This could include soaking, scrubbing, or spraying, depending on the equipment type.
- Post-Cleaning: Rinse (if necessary) and dry the equipment to prevent any damage or microbial growth. Inspect the equipment to ensure it meets the required cleanliness standards.
During these processes, always prioritize safety precautions to protect both staff and patients. Use gloves, masks, and other protective gear as needed. Be mindful of handling both disposable and reusable components carefully to avoid cross-contamination.
Selection and Use of Approved Cleaning Agents
Choosing the right cleaning agents is crucial for effective disinfection while maintaining the integrity of the DME. Consider the following when selecting a cleaning agent:
- Pathogen Efficacy: Ensure the agent is effective against the types of pathogens likely to be encountered.
- Material Compatibility: Check that the agent won’t degrade the equipment materials over time.
- Safety: The agent should be safe for use around patients and staff, with minimal toxic effects.
- Environmental Impact: Opt for agents that offer lower environmental impact without compromising on efficacy.
- Cost-Effectiveness: Balance quality and cost, considering the frequency of use and the required quantities.
Using the right agents not only extends the lifespan of your equipment but also ensures safety and compliance with health standards.
Ensuring Compliance with Regulatory Standards
Staying compliant with regulatory standards is not just about following rules—it’s about ensuring the highest level of patient safety and care. Familiarize yourself with the guidelines set by bodies such as the CDC and FDA. Here’s how to integrate these standards into your cleaning protocols:
- Regular Audits: Conduct audits to ensure your cleaning practices meet all required standards.
- Staff Training: Provide ongoing training for your staff to keep them informed about the latest regulations and best practices.
- Documentation: Keep detailed records of cleaning schedules, procedures, and compliance checks.
By embedding these practices into your daily operations, you can maintain a high standard of hygiene and safety, ensuring that your facility remains compliant and your patients stay safe.
Training and Compliance in DME Hygiene
Effective DME hygiene management hinges significantly on the quality of staff training. Ensuring that all team members understand and adhere to the proper use, cleaning, and maintenance of durable medical equipment is crucial. This section delves into developing robust training programs, evaluating their effectiveness, and maintaining compliance with evolving hygiene standards. Emphasis is also placed on the necessity for continuous education and staying updated with new cleaning technologies and standards.
Developing Effective Training Programs for Staff
Creating comprehensive training programs for healthcare facility staff involves both theoretical knowledge and practical application. Here’s how to ensure these programs are effective:
- Outline Clear Objectives: Start with clear learning objectives that cover the importance of DME cleaning, the risks associated with improper practices, and the benefits of adherence to protocols.
- Comprehensive Content: Include detailed cleaning procedures, proper use of cleaning agents, and techniques for ensuring thorough disinfection.
- Practical Training: Incorporate hands-on sessions where staff can practice the skills they’ve learned, using the actual equipment they will be handling.
- Assessment and Competency Checks: Regularly assess staff competency through quizzes, practical tests, and performance evaluations.
- Ongoing Support and Refreshers: Provide continuous learning opportunities and updates on new procedures or equipment to maintain high standards of hygiene.
By focusing on these elements, training programs can effectively prepare staff to manage DME hygiene proficiently, ensuring safety and compliance.
Monitoring and Documenting Adherence to Cleaning Protocols
To ensure that cleaning protocols are consistently followed, it is essential to monitor and document adherence effectively. Utilizing checklists, digital logs, and audit tools can help in maintaining rigorous standards. Here’s how these tools can be integrated:
- Checklists: Develop daily, weekly, and monthly cleaning checklists for different types of equipment. This helps ensure that no aspect of the cleaning protocol is overlooked.
- Digital Logs: Use digital tools to record cleaning activities. These logs can provide real-time data and insights into the adherence levels and pinpoint areas needing improvement.
- Audit Tools: Implement regular audits using standardized tools to evaluate compliance with cleaning protocols. Audits help identify gaps in training or execution and provide a basis for corrective actions.
- Documentation for Compliance: Maintain detailed records as part of regulatory compliance. Documentation should include training records, cleaning schedules, audit results, and updates to procedures.
These monitoring and documentation practices not only help in ensuring compliance with hygiene standards but also play a critical role in quality control and continuous improvement processes.
Leveraging Technology for Efficient DME Management
In today’s fast-paced healthcare environment, leveraging advanced technology is key to enhancing the management and hygiene of Durable Medical Equipment (DME). Technologies like MasVida’s OneSource Healthcare Equipment Portal not only streamline operations but also boost compliance, efficiency, and patient safety. This section explores how integrating technology can transform DME management by facilitating real-time tracking, automated scheduling, and seamless system integration.
Utilizing MasVida’s OneSource Healthcare Equipment Portal for Real-Time Management
MasVida’s OneSource portal is a game-changer for healthcare facilities, offering a comprehensive solution for managing DME cleaning schedules and inventory. Here’s how it enhances DME management:
- Inventory Tracking: Keep a real-time tab on all DME assets, ensuring that nothing goes unaccounted for.
- Usage Analytics: Gain insights into how equipment is being used, which can help in optimizing purchase and maintenance decisions.
- Maintenance Alerts: Receive automated notifications for upcoming maintenance and cleaning schedules, ensuring no task is overlooked.
The integration of these features into a single integrated platform simplifies the management process, making it more efficient and less prone to errors. This consolidation helps facilities maintain high standards of hygiene and equipment readiness, directly impacting patient care quality.
Integrating DME Management with Facility-Wide Hygiene Practices
Effective DME management is not an isolated task—it should be part of a broader strategy encompassing overall facility hygiene and infection control. Here’s how integrating these practices can lead to better health outcomes and operational efficiency:
- Department Coordination: Ensures that all departments work in sync when it comes to hygiene and equipment management, leading to more cohesive and effective practices.
- Role of DME in Facility Hygiene: Properly maintained and sanitized DME is crucial in preventing infection spread within the facility.
- Impact on Health Outcomes and Operational Efficiency: Integrated practices not only improve patient safety but also enhance the overall operational efficiency by reducing equipment downtime and associated costs.
Examples of successful integration show significant improvements in patient care quality and reductions in healthcare-associated infections, underlining the importance of holistic management approaches.
Advantages of Partnering with MasVida for DME Needs
Partnering with MasVida Health Care Solutions for your Durable Medical Equipment (DME) management and hygiene needs brings a host of strategic benefits. MasVida’s comprehensive services, including same-day delivery, extensive equipment offerings, and advanced infection prevention products, are designed to enhance the efficiency and effectiveness of your DME hygiene practices. This partnership underscores MasVida’s commitment to reliability, transparency, and exceptional customer support.
Benefits of MasVida’s Same-Day DME Delivery Service
MasVida’s same-day delivery service is a game-changer for healthcare facilities, ensuring that essential medical equipment is always at hand when needed. Here are some key advantages:
- Immediate Equipment Access: Quick delivery ensures that facilities can maintain continuous care without interruptions, even in urgent situations.
- Geographic Coverage: MasVida reliably serves facilities across Texas, Oklahoma, and Louisiana, making it a dependable partner regardless of location.
- Delivery Reliability: With a commitment to on-time delivery, MasVida helps facilities meet their care standards consistently, enhancing patient satisfaction.
This service is particularly valuable in emergency scenarios where the availability of medical equipment can significantly impact patient outcomes.
Enhancing DME Hygiene with MasVida’s Infection Prevention Solutions
MasVida’s infection prevention and control solutions are integral to maintaining high standards of hygiene in DME management. These solutions include a range of products that are both effective and easy to use, ensuring that your facility can uphold top-notch hygiene practices. Key aspects include:
- Product Range: MasVida offers everything from disinfectants to specialized cleaning equipment, designed to meet the rigorous demands of healthcare environments.
- Infection Control: These products are proven to reduce the risk of infection, supporting your facility’s health and safety protocols.
- Integration with Cleaning Protocols: MasVida’s solutions complement existing DME cleaning schedules, enhancing their effectiveness and ensuring comprehensive hygiene maintenance.
- Cost-Effectiveness: With competitive pricing and bundled options, MasVida’s solutions are both affordable and efficient, reducing overall hygiene maintenance costs.
By integrating these advanced products into your DME hygiene practices, you not only safeguard the health of your patients but also enhance the operational efficiency of your facility.
Join healthcare’s ultimate resource for long-term care!
Never miss out on our podcast, blogs, or daily content created to educate, equip, and encourage long-term care leaders to provide better care to the growing population of over eight million seniors in the U.S.
• Follow Us on Linkedin
• Join our weekly Newsletter
OneSource: Your Single Source for Same-day DME Delivery and Better Facility Hygiene
Better products. Better service. Better outcomes.
Partnering with one provider for your DME and facility hygiene services can result in reduced turnover, higher quality work, and healthier facilities.
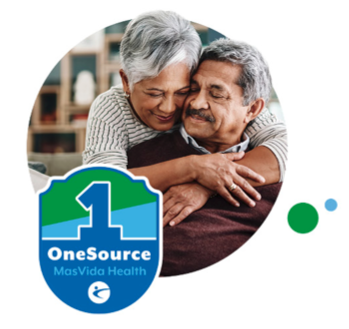

Medical OxygenTherapy →
Negative Pressure (NPWT) →
Respiratory Therapy →
Durable Medical Equipment →